SCIENCE
Thien eDrives Cuts Electric Motor Controller Development Time in Half with Model-Based Design
MathWorks today announced that Thien eDrives (formerly ATB Technologies), a developer of electrical drive systems, used MATLAB and Simulink to model, simulate, and implement an electric motor control system on TI’s C2000 microcontroller unit (MCU). By applying Model-Based Design, Thien eDrives moved rapidly from the first prototype to the final series, reducing development time by 50%.
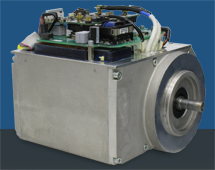
To develop an electric drive for a fuel cell vehicle compressor unit, including the motor control software, electronics, motor, and other mechanical components, Thien eDrives needed a design approach that enabled early verification of control strategies, code generation, and rapid design iterations throughout the project. Model-Based Design allowed for verification at multiple stages of development, helping produce a high-quality component within a shortened timeframe. Automatic code generation eliminated the time-consuming and error-prone hand-coding process while providing added confidence of compliance with certain MISRA C standards. Using models also simplified design reviews with Thien eDrives customers by eliminating the need for code review-driven processes.
“On past projects, we simulated and verified our designs in Simulink,” says Georg Staffler, development engineer at Thien eDrives. “For this project, we adopted automatic code generation, which enabled us to complete the compressor project twice as fast as a similar project that applied Model-Based Design with hand coding. Code generation resulted in fewer bugs, better quality, and faster iterations, and it enabled a modular approach that facilitated model reuse across projects.”
“Electric drive projects are becoming more complex as they require the many components within a system to work together for maximum performance and efficiency,” says Jon Friedman, automotive industry marketing manager at MathWorks. “Model-Based Design offers a workflow that enables engineers to work on the design at both the component level and the overall application level. Thien eDrives showcases how this design approach brings efficiencies and advantages to every stage of the development process.”
In addition to MATLAB and Simulink, the team used other tools, including Simulink Coder,Embedded Coder, Stateflow, Signal Processing Toolbox, and Simulink Fixed Point. Model-Based Design enabled Thien eDrives to deliver the compressor motor on schedule, and the motor is currently produced and embedded in fuel cell cars on the road today.
More details on the use of MATLAB and Simulink at Thien eDrives can be found at: ATB Technologies Cuts Electric Motor Controller Development Time by 50% Using Code Generation for TI’s C2000 MCU.
